PortMiami trademarks itself as the “Cruise Capital of the World”, with more than 5.5 million passengers passing through each year. It is a thriving cargo port accounting for more than 300,000 jobs and a vital economic driver for the State of Florida.
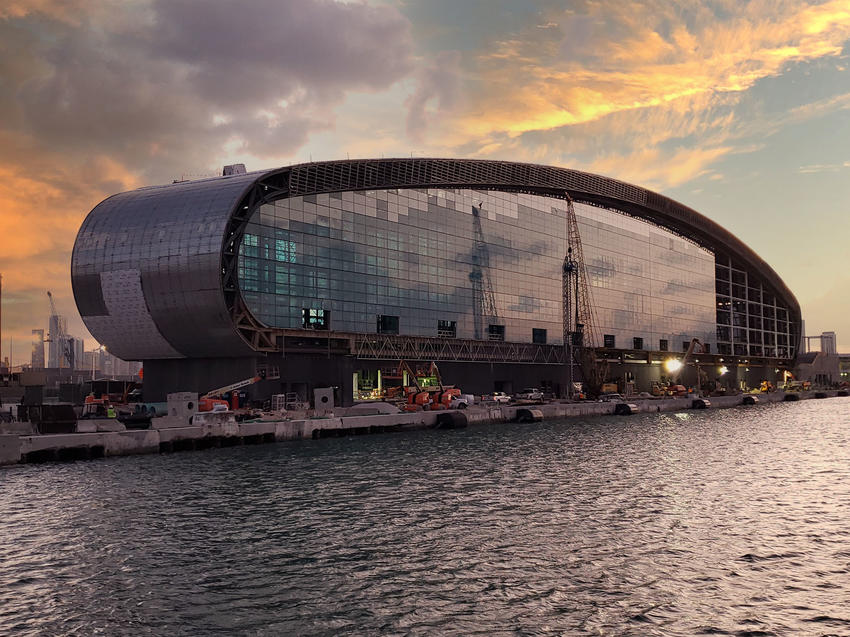
The project
Several new terminals for PortMiami are being constructed, including Terminal B, named the Pearl of Miami, exclusively accommodating Norwegian Cruise Line vessels.
The first phase of construction for Terminal B includes the terminal building itself, a warehouse, and a parking garage, all to be constructed atop a subsurface profile consisting of up to 35 ft of fill material over limestone bedrock. Auger cast pile foundation systems were recommended by the Geotechnical Engineer for the project and Keller was awarded the contract for the work.
The challenge
The high-profile project presented several challenges, both to the owner and to Keller:
- The owner established an aggressive schedule for the completion of the Phase 1 construction to meet the planned terminal opening date. Because of this, the general contractor prepared a specific foundation schedule.
- Multiple contractors working alongside each other led to a very congested site.
- Site constraints meant that Keller had to set up an off-site steelyard and deliver the prefabricated steel reinforcing cages to the site as needed.
The solution
Given the accelerated schedule, the owner decided to begin work before the foundation design had been completely finalized. Keller assumed a consultant’s role in addition to the foundation contractor. Keller engineers offered experience-based recommendations on the redesign, including the use of a uniform pile depth of 52 ft for the terminal and warehouse buildings’ 16-in. diameter piles, rather than the customized, location-based pile depths originally specified. This reduced material costs and installation times. The parking structure foundation was completed as designed, using the specified 14-in. and 18-in. diameter auger cast piles.
Prior to production work, load tests were conducted on three groups of sacrificial piles to verify anticipated pile performance. Spoil generated during the production piling was regularly trucked off-site. Reinforcing cages were delivered to the site from the steelyard as needed, with tension piles receiving full-length cages while compression piles received full cages for the top 30-35 ft, tapering to a central bar down to the required tip elevation.
Because of Keller’s redesign and operational efficiency, the Phase 1 foundation work, consisting of over 1,400 piles, was completed two months ahead of schedule.

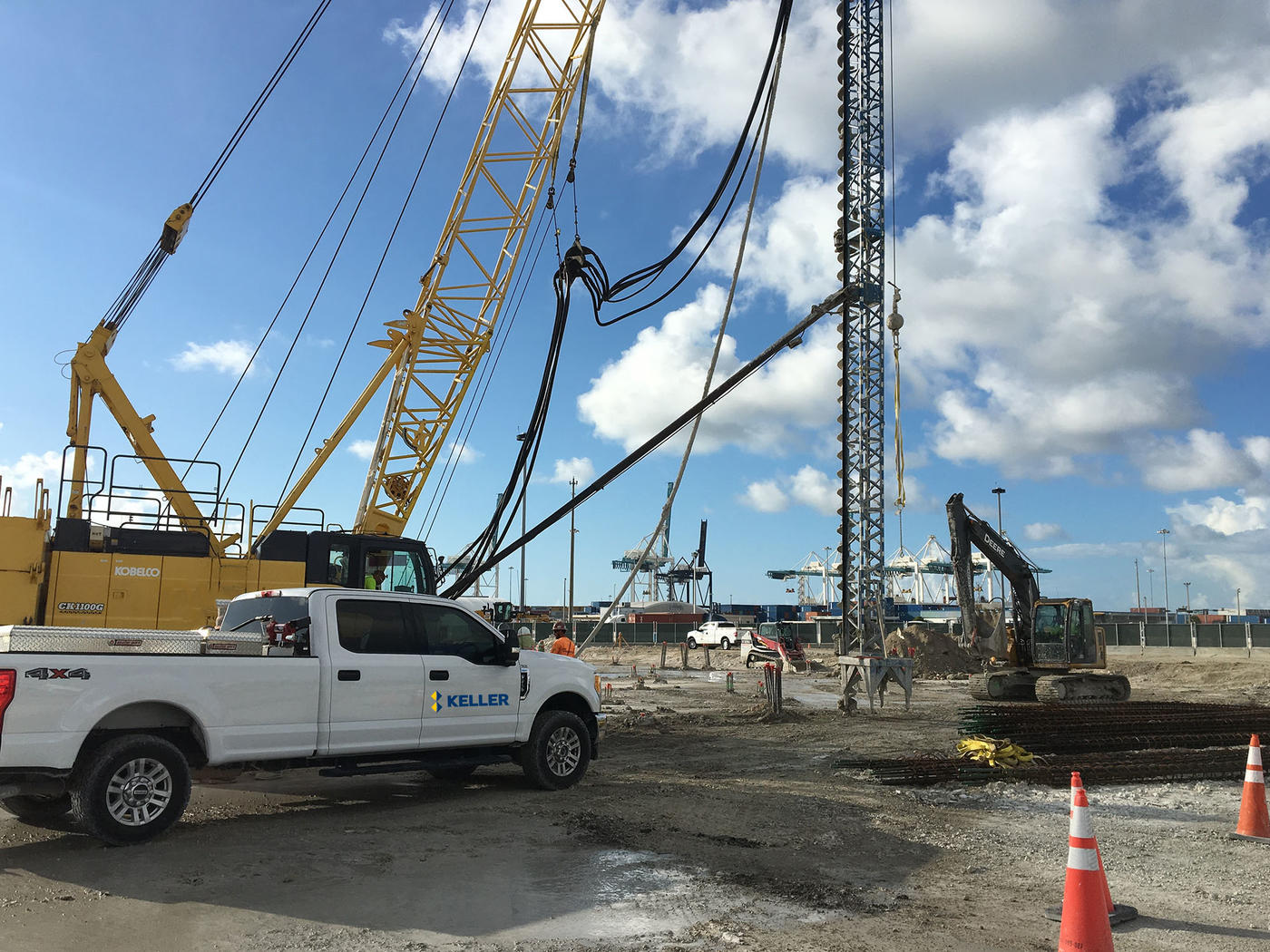